Aerospace
Magnesium: The Lightweight, Versatile, and Sustainable Metal
Magnesium is the lightest structural metal, with a density of only 1.74 grams per cubic centimeter. This makes it 33% lighter than aluminum and 75% lighter than steel. Magnesium is also easily formed and can be dry free machined with less power, more speed, and less tool wear. It can also be TIG, MIG, and friction stir welded.
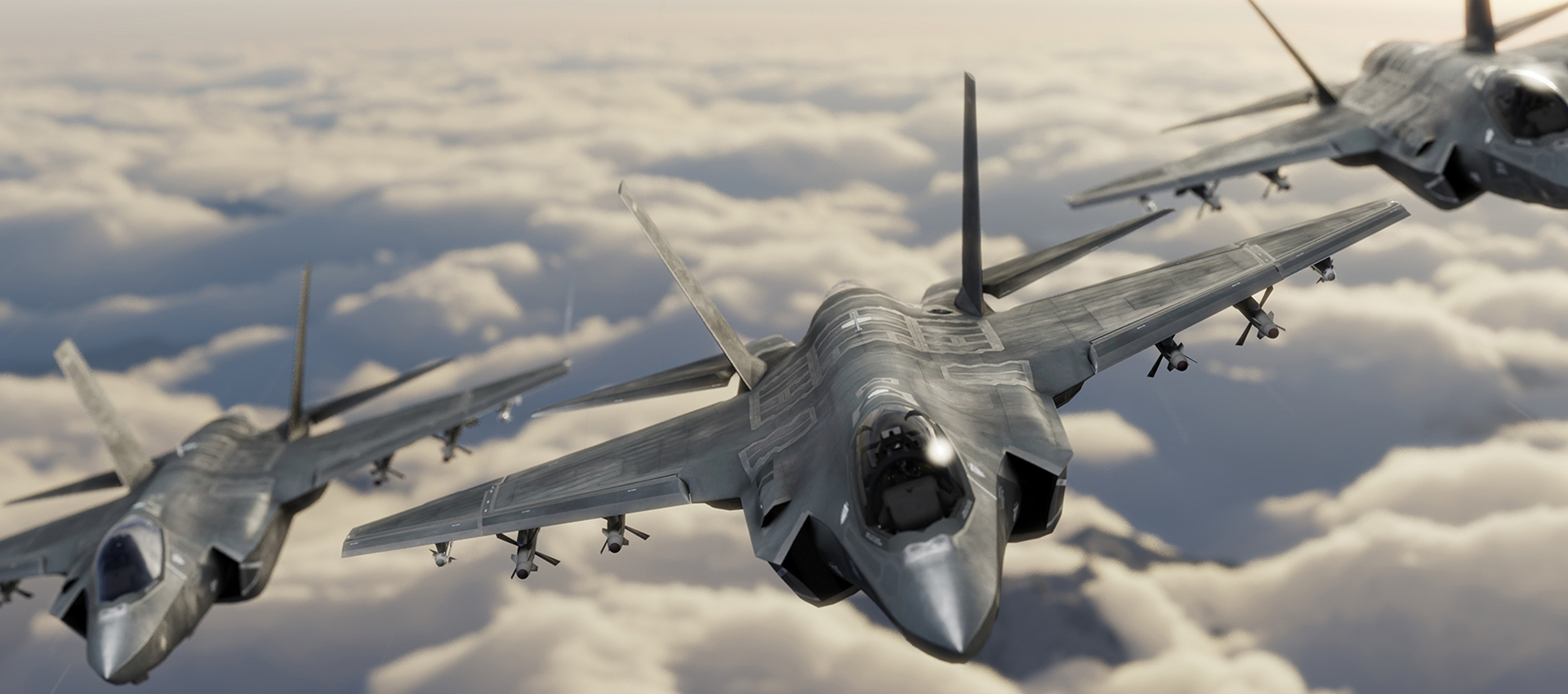
Modern magnesium alloys have enhanced corrosion resistance, making them suitable for a wide range of applications. Magnesium is the 8th most abundant element in the Earth’s crust and the 3rd most plentiful element found in seawater.
Magnesium is also highly formable, even at relatively low temperatures of 300 degrees Celsius. This makes it ideal for applications where complex shapes and deep draws are required. Magnesium is also more dent-resistant than aluminum sheet, making it a good choice for automotive panels, cell phones, laptops, and camera cases.
Magnesium is also non-toxic and alkali-resistant. In normal atmospheres, the corrosion rate of uncoated magnesium is lower than iron or steel. In severe environments, superior coating and finishing systems are available to prevent galvanic corrosion of magnesium components.
Magnesium is an environmentally friendly metal. It is virtually limitless, with abundant supplies in seawater. Magnesium is also endlessly recyclable at only 5% of the initial refinement energy, without degradation of properties.
Benefits of magnesium for aerospace applications
Magnesium offers a number of benefits for aerospace applications, including:
Lightweight
Magnesium is the lightest structural metal available, making it ideal for aerospace applications where weight reduction is essential. Reducing the weight of an aircraft or spacecraft can lead to significant fuel savings and increased range.
Strong
Magnesium alloys are very strong, even at high temperatures. This makes them ideal for use in aerospace components that are subjected to high stresses, such as landing gear, engine components, and structural members.
Durable
Magnesium alloys are also very durable and can withstand the harsh environment of the atmosphere, including exposure to radiation and extreme temperatures.
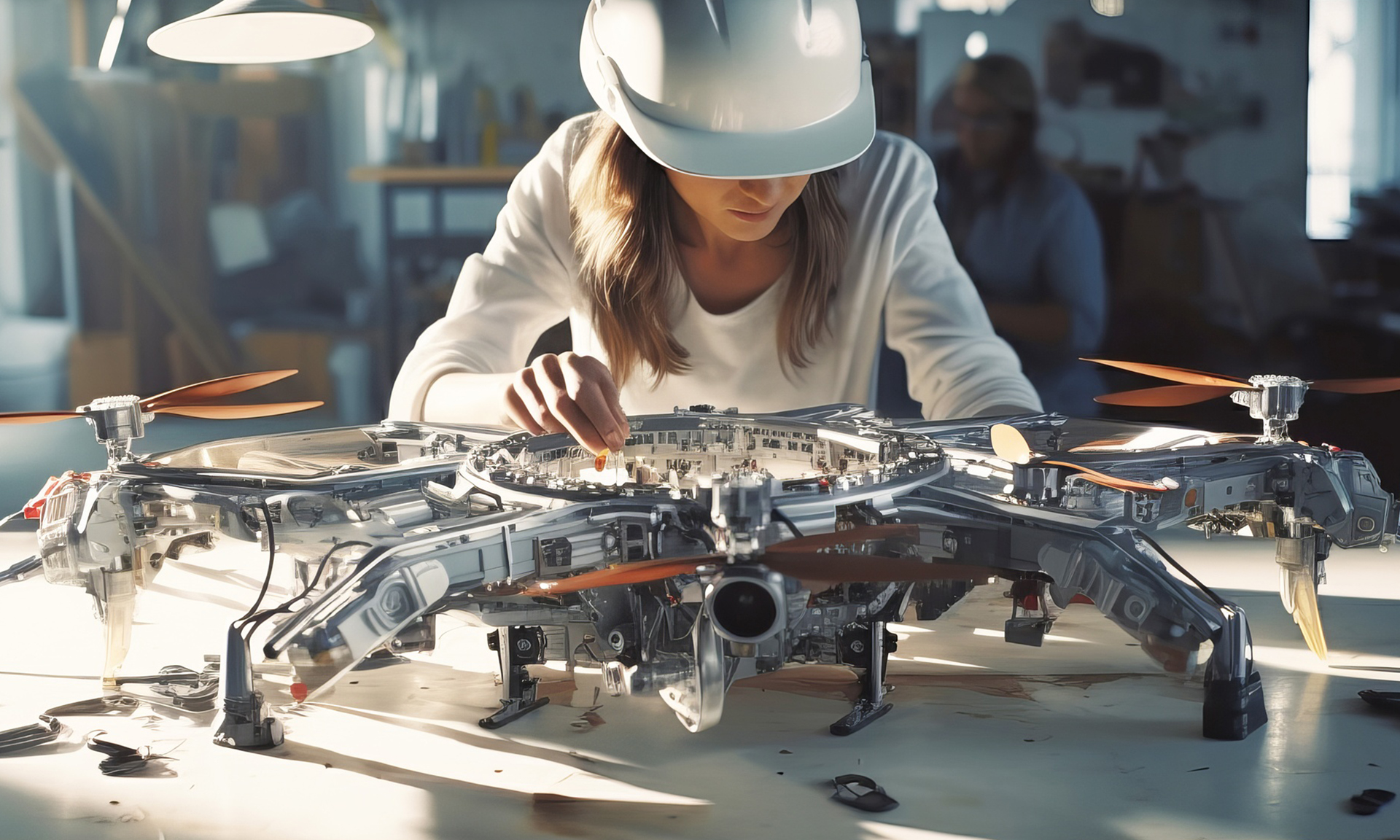
Applications of magnesium in aerospace
Magnesium is used in a wide variety of aerospace applications, including:
Aircraft skins: Magnesium sheets are used in the construction of aircraft skins, which provide aerodynamic performance and protect the internal components of the aircraft.
Aircraft engines: Magnesium alloys are used in a variety of aircraft engine components, such as compressor blades, turbine disks, and crankcases.
Airframe components: Magnesium alloys are used in a variety of airframe components, such as wing spars, fuselage frames, and landing gear.
Spacecraft components: Magnesium alloys are used in a variety of spacecraft components, such as satellite structures, solar panels, and rocket casings.
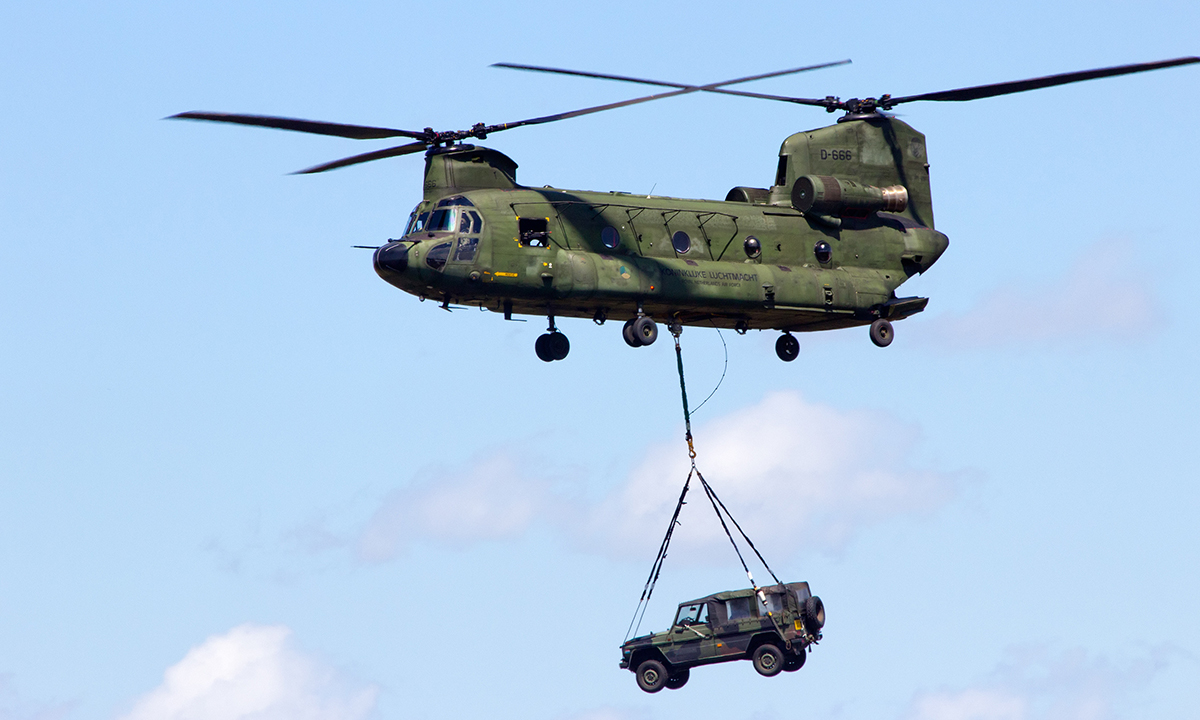
Case studies
Here are a few examples of successful applications for magnesium in the aerospace industry:
F-35 multirole fighter jet: The F-35 multirole fighter jet uses magnesium components in its wings, fuselage, and landing gear.
Chinook helicopter: The Chinook helicopter uses magnesium components in its rotors, fuselage, and landing gear.
International Space Station: The International Space Station uses magnesium components in its solar panels, radiator panels, and truss structure.