Why Magnesium
Magnesium is the lightest structural metal, with a density of only 1.74 grams per cubic centimeter. This makes it 33% lighter than aluminum and 75% lighter than steel. Magnesium is easily formed and can be dry free machined with less power, more speed, and less tool wear. It can be TIG, MIG, and friction stir welded.
Modern magnesium alloys have enhanced corrosion resistance, making them suitable for a wide range of applications. Magnesium is the 8th most abundant element in the Earth’s crust and the 3rd most plentiful element found in seawater.
Magnesium is highly formable, even at relatively low temperatures of 300 degrees Celsius. This makes it ideal for applications where complex shapes and deep draws are required. Magnesium is more dent-resistant than aluminum sheet, making it a good choice for automotive panels, cell phones, laptops, and camera cases.
Magnesium is non-toxic and alkali-resistant. In normal atmospheres, the corrosion rate of uncoated magnesium is lower than iron or steel. In severe environments, superior coating and finishing systems are available to prevent galvanic corrosion of magnesium components.
Magnesium is an environmentally friendly metal. It is virtually limitless, with abundant supplies in seawater. Magnesium is forever recyclable at only 5% of the initial refinement energy, without degradation of properties.
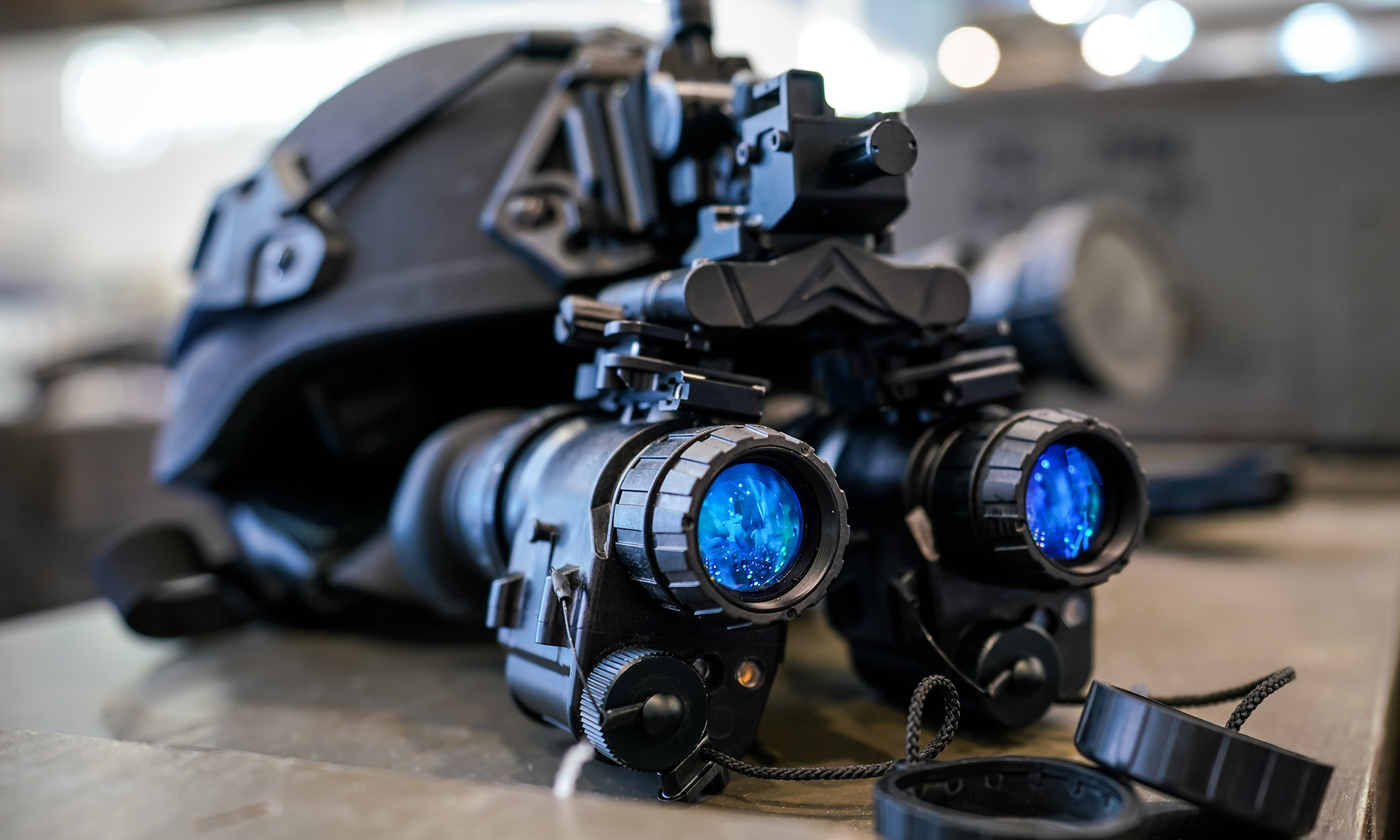
Applications of Magnesium
Magnesium is used in a wide variety of sectors, including:
- Aerospace: Magnesium is used in aircraft and spacecraft components due to its lightweight and high strength properties.
- Automotive: Magnesium is used in automotive parts such as engine blocks, wheels, and body panels to reduce weight and improve fuel efficiency.
- Consumer electronics: Magnesium is used in consumer electronics such as laptops, cell phones, and cameras due to its lightweight and sleek design properties.
- Medical: Magnesium is used in medical implants and devices due to its biocompatibility and non-toxic properties.
- Sea Water Battery: Magnesium seawater batteries helps powering underwater drones, autonomous submarines, and other marine research equipment.
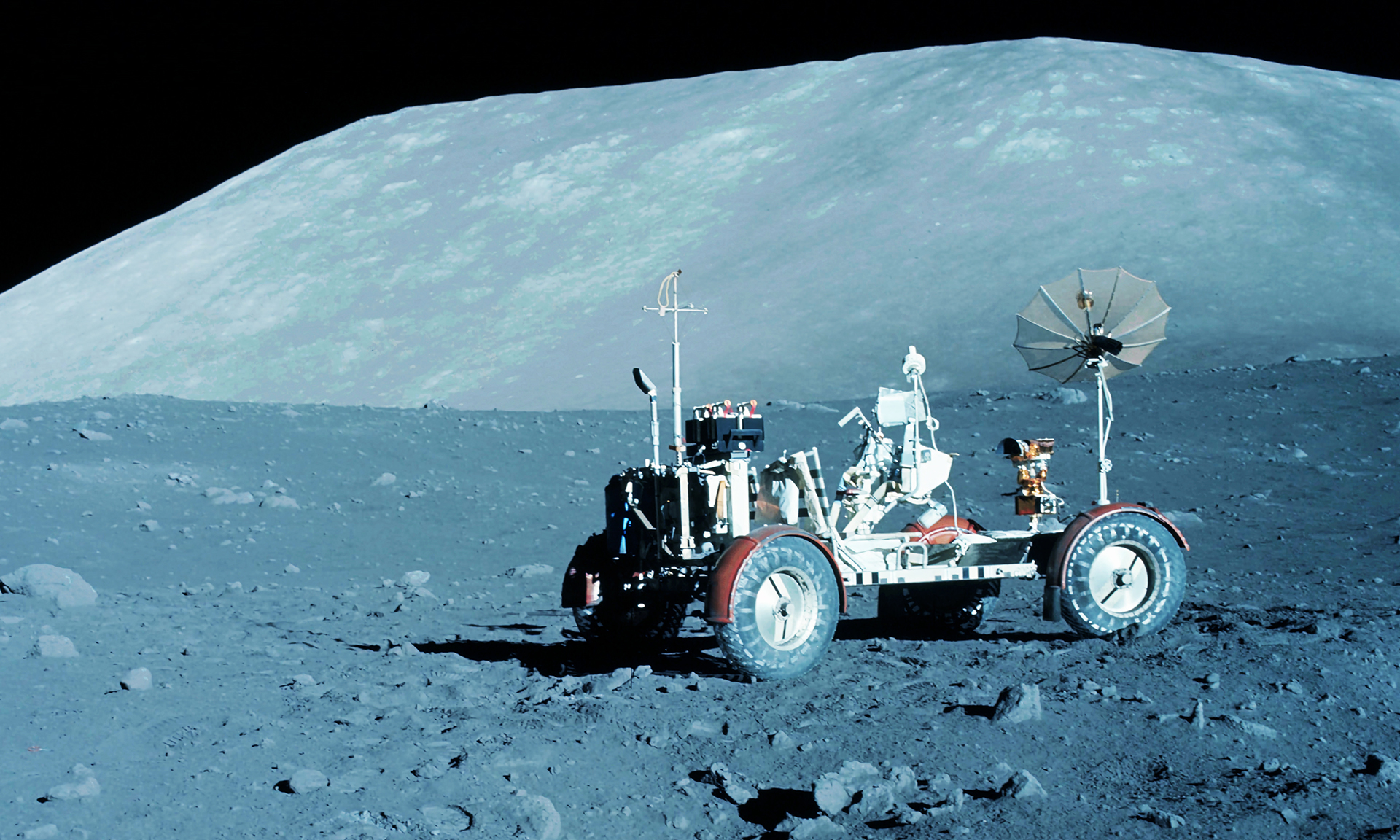
Benefits of Magnesium
Magnesium offers a number of benefits, including:
- Lightweight: Magnesium is the lightest structural metal, making it ideal for applications where weight reduction is critical.
- Strong: Magnesium alloys are very strong, even at high elevated temperatures and under high stresses.
- Recyclable: Magnesium is a highly recyclable metal, which helps to reduce its environmental impact.
- Sustainable: Magnesium is a sustainable metal, with abundant supplies in seawater and the ability to be recycled endlessly without degradation of properties.
Features | AL 6061 | AZ31B-H24 | Elektron 43 |
Chemical Composition | Magnesium: 0.8-1.2% | Aluminum: 2.5-3.5% | Yttrium: 3.7 4.3% |
Silicon: 0.4-0.8% | Zinc: 0.7-1.3% | Rare Earths: 2.3-3.5% | |
Copper: 0.15-0.40% | Manganese: 0.20-1.0% | Zirconium: 0.2% min | |
Aluminum: Balance | Magnesium: Balance | Magnesium: Balance | |
Physical Properties | |||
Specific Gravity | 0.098 lbs/in3 (2.72g/cm3) | 0.064 lb/in3 (1.78g/cm3) | 0.068 lbs/in3 (1.83g/cm3) |
Coefficient of thermal Expansion | 12.5× 10-6°F (68.37 × 10-6K) | 4.9 × 10-6°F (26.8 × 10-6K) | 4.7 × 10-6°F (25.6 × 10-6K) |
Specific Heat | 0.22 Btu/lb/°F (915.2 J/kg/K) | 0.25 Btu/lb/°F (1040 J/kg/K | 0.24 Btu/lb/°F (993 J/kg/K) |
Thermal Conductivity | 83 Btu/hr/ft2/°F (143.4 W/m2/K) | 44.5 Btu/hr/ft2/°F (76.9 W/m2/K) | 33.3 Btu/hr/ft2/°F (57.6 W/m2/K) |
Electrical Resistivity | 3.99 × 10-6 ohm-cm | - | - |
Modulus of Elasticity | 68.9 GPa | 44 GPa | 44 GPa |
Poissons Ratio | 0.33 | 0.35 | 0.295 |
Melting Range | 1080-1205°F (582-652°C) | 1050-1170°F (566-632°C) | 1004-1184° F (540 - 640° C) |
Density | |||
Elastic Modulas | |||
Fracture Elongation | 10% | 8% | 12% |
Tensile Yield Strength | 36ksi | 22ksi | 33ksi |
Corrosion Rate | N/A | N/A | N/A |
Welding Capability | Excellent weldability with gas shielded arc using AZ61A (preferred) or AZ92A filler rod; post weld stress relief is required to prevent stress corrosion cracking. AZ31B sheet and plate can also be FSW | ||
Oxidation/Corrosion | The surface protection of AZ31B is dependent on the service conditions where the material will be operating. In dry conditions, with limited exposure to moisture, AZ31B can be left bare or lightly oiled. A protective coating solution should be given to application in more demanding environments. AZ31B can be protected by a variety of coatings that include chromating, anodizing, plating, e-coat, paint, and plasma electrolytic oxidation (PEO). It is recommended to prepare the magnesium surface by cleaning and pre-treatment (conversion coating) using traditional non-ferrous methods prior to e-coat or paint. There are commercially available pre-treatments that are a non-chromate based chemistry which result in good adhesion of the paint system | The surface protection of Elektron 43 is dependent on the service | |
Specifications | AZ31B meets these specifications: AMS 4377, AMS 4375, AMS 4382 and ASTM B90 |